Case Study 2
Biodiesel derived from Category 1 & 2 fat – Daka ecoMotion, Denmark
Products derived from higher risk Category 1 and 2 ABP have limited applications and their use is forbidden in feed for farmed animals kept for the production of meat, milk and eggs. Similarly, catering waste is prohibited for feed use which includes used cooking oils (UCO).
Biodiesel production is an EFSA (European Food Safety Authority) approved safe process and is a recognised alternative an alternative method to rendering for processing Category 1 and 2 fats and oils. Unlike clear vegetable oils such as soy and rape oil or palm fat, animal fats and UCO contain difficult to remove impurities such as fatty acids, polyethylene and sulphur.
To address this the biodiesel process is more complex with pre-treatment and cleaning steps to produce certified standard biodiesel.
Under the Renewable Energy Directive, biodiesel produced from animal residues and by-products from agriculture and slaughterhouses is classified as “Second Generation” biofuel (2G). Unlike the less sustainable “first generation” biofuels made from food and feed grade crops, 2G Biofuel is one of the most environmentally friendly and sustainable biodiesels on the market today. 2G biofuels derived from these materials have 83% less CO2 emissions than fossil diesel (calculated according to EU-ISSC-CERT 2020).
2G biofuels derived from these materials have 83% less CO2 emissions than fossil diesel
Daka ecoMotion in Denmark produces over 50 million litres of biodiesel from Category 1 and 2 fats per year which is blended with fossil diesel for various transport fuel applications. In 2020, LCA Consultants and Aalborg University prepared an independent life cycle analysis of all the Daka ecoMotion activities to assess their products’ environmental impact from cradle to grave.
It was found that replacing fossil fuels with 2G biodiesel from ecoMotion eliminates around 270,000 tonnes CO2 equivalents per year. This is almost 7.5 times Daka ecoMotion’s own transport and production emissions which have been optimised through systematic energy
management in line with ISO 50001.
Since 2016 their emissions have reduced by around 17% through energy efficiency investments such as heat recovery, vacuum and steam optimisation, energy efficient lighting and cooling tower improvements. Water consumption has also been reduced by 31% since 2016 with further scope for reductions under review.
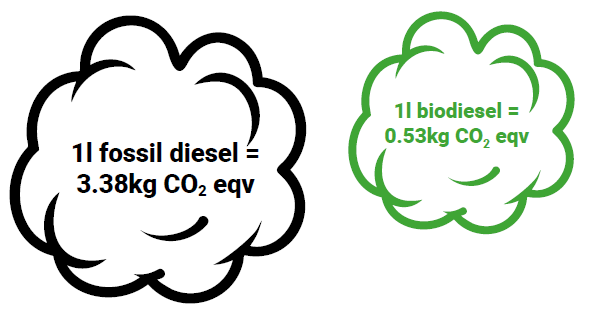
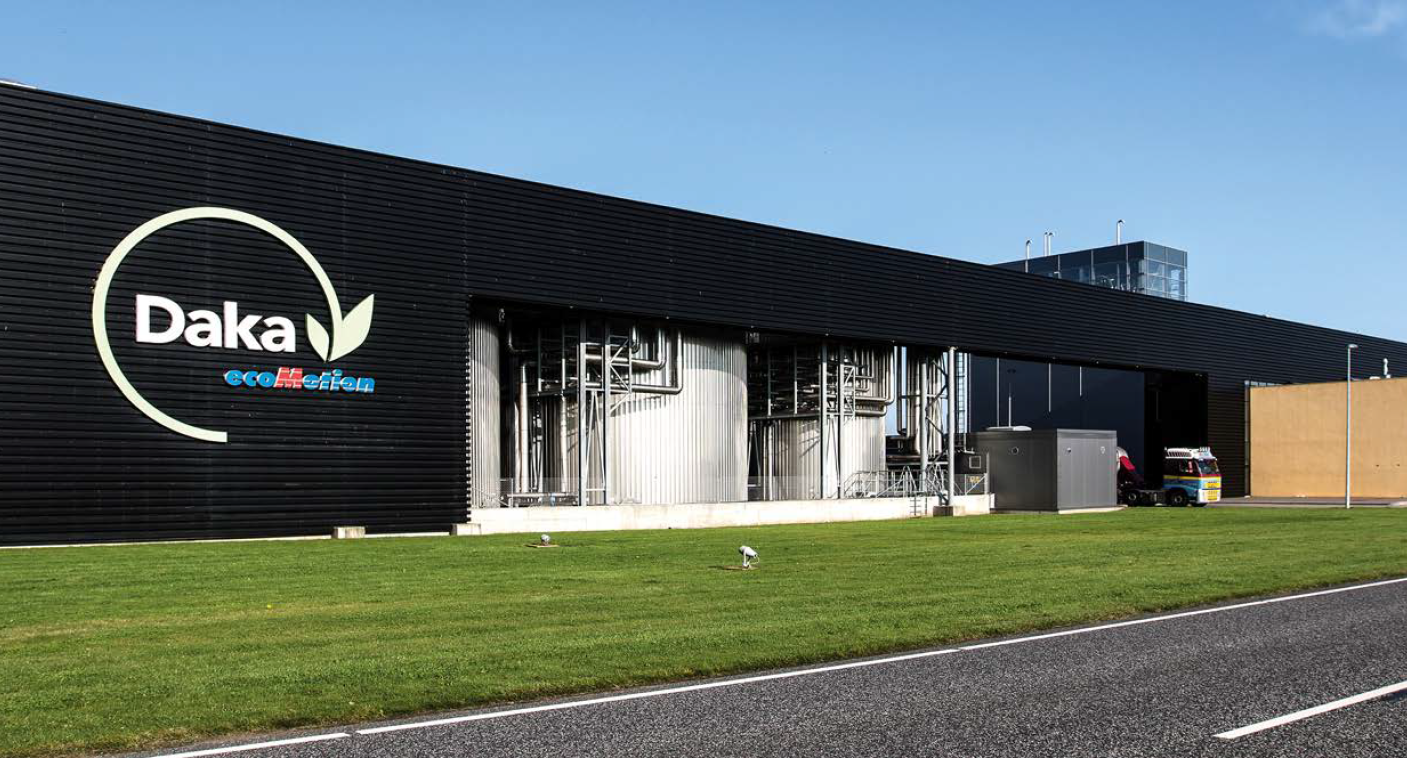
Case Study 2 - Version 1, October 2021